- Home /
- About Us
Plant in Italy
screenshot_region
60.000 m²Total areascreenshot_region
crop_square
warehouse
30.600 m²Dedicated to warehousingengineering
7.000People working in associated companiesgroups
400Employed personneldeployed_code
26.000Units sold per day (footwear, clothing, dozens of gloves, dozens of glasses, dozens of masks)Plant in Albania
screenshot_region
40.000 m²Total areascreenshot_region
crop_square
group_add
1800People directly employedsteps
10.000Pairs of footwear produced every day
History
The company was founded in 1938 in Barletta under the name Cortelgomma by Ruggiero Cortellino. Shortly after the war, the artisanal workshop began producing shoes with soles made from military truck tires and uppers made from military uniforms. The founder's entrepreneurship and passion transformed it into a modern enterprise capable of producing hundreds of pairs of shoes per day, distributed throughout Italy.
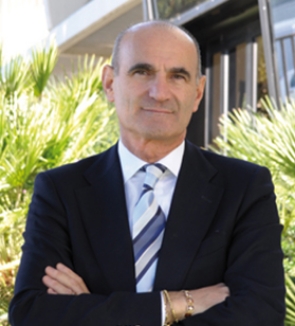
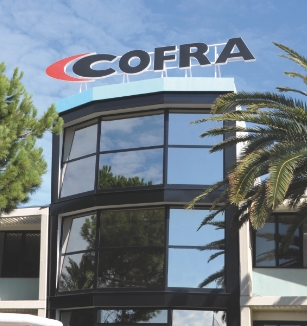
In 1983, it became COFRA and is currently managed by Giuseppe Cortellino, the founder's son, and the internationalization process of the company began. Its continuous growth is the result of careful entrepreneurial management and innovative managerial culture, making the company a market leader in the professional footwear sector, recognized brand throughout Europe and the rest of the world. Diversification and product range expansion began in 2004.
The production processCOFRA controls the entire production process, ensuring high-quality standards.
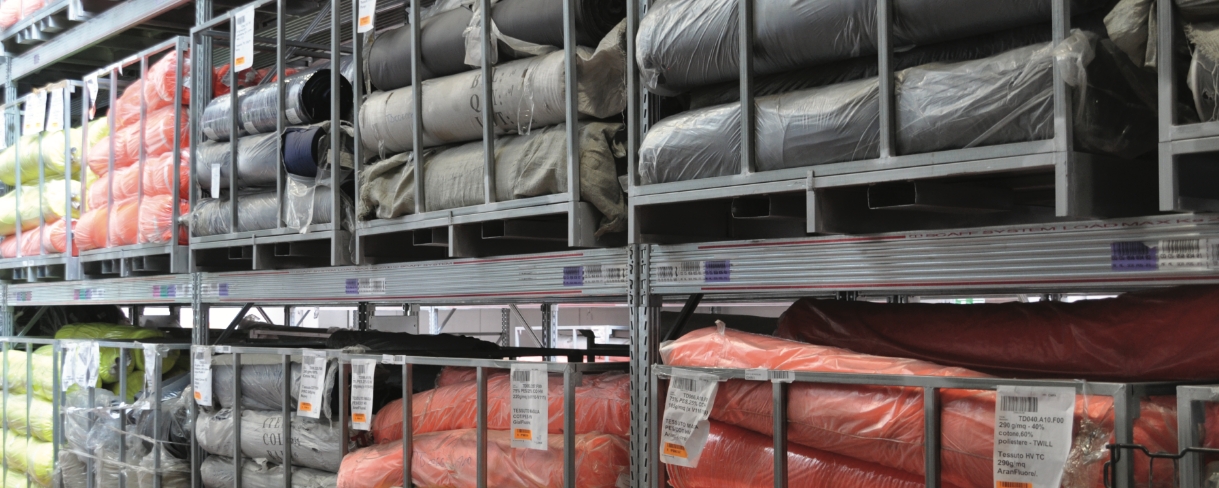
Selection of raw materialsThe production phase starts with the acquisition of raw materials, carefully selected and subjected to internal acceptance tests to ensure their compliance with quality standards.
The laboratoriesLaboratory tests: two in-house laboratories, one chemical and one physical, perform all necessary tests on both raw materials and finished products for subsequent certification by authorized bodies.
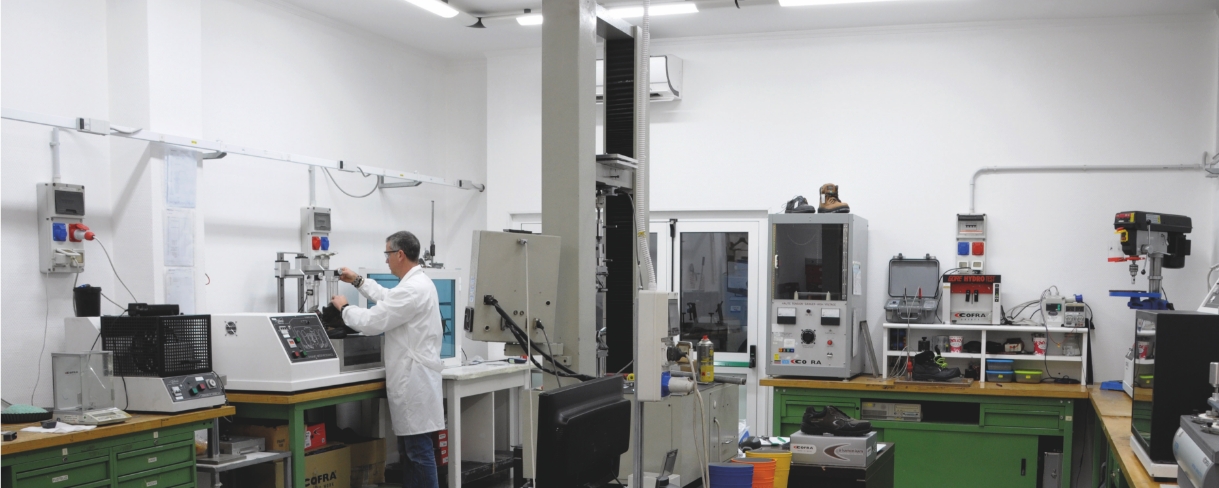
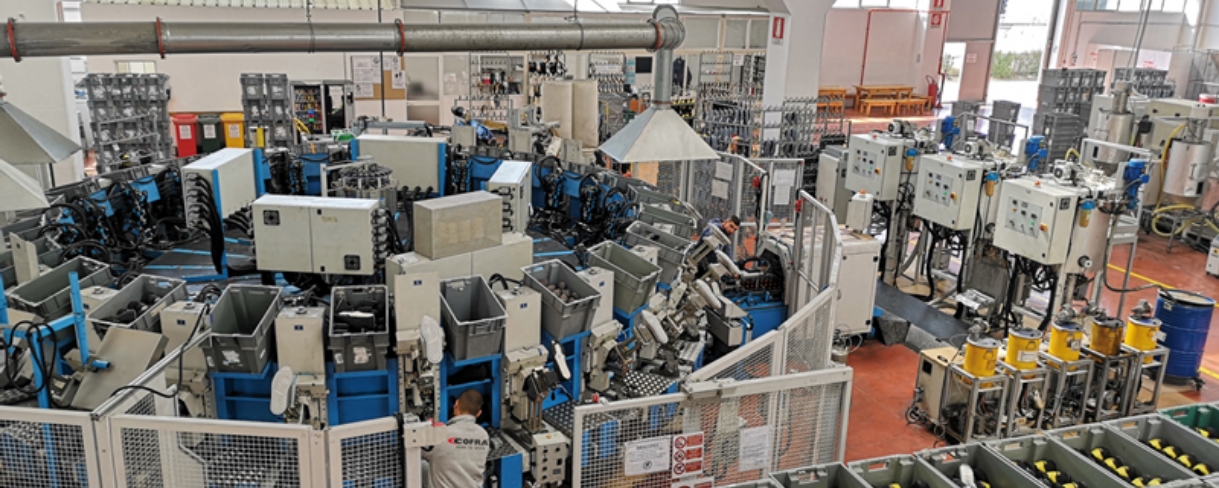
Production plant1,100 people employed directly in upper production. 600 people employed directly for sole application.
Production facilitiesNine direct injection rotating machines, with the assistance of applied anthropomorphic robots integrated with the rotatives themselves, are managed and adapted to individual production needs. Three rotating machines are dedicated to producing rubber and thermoplastic polyurethane (TPU) tread up to four colors.
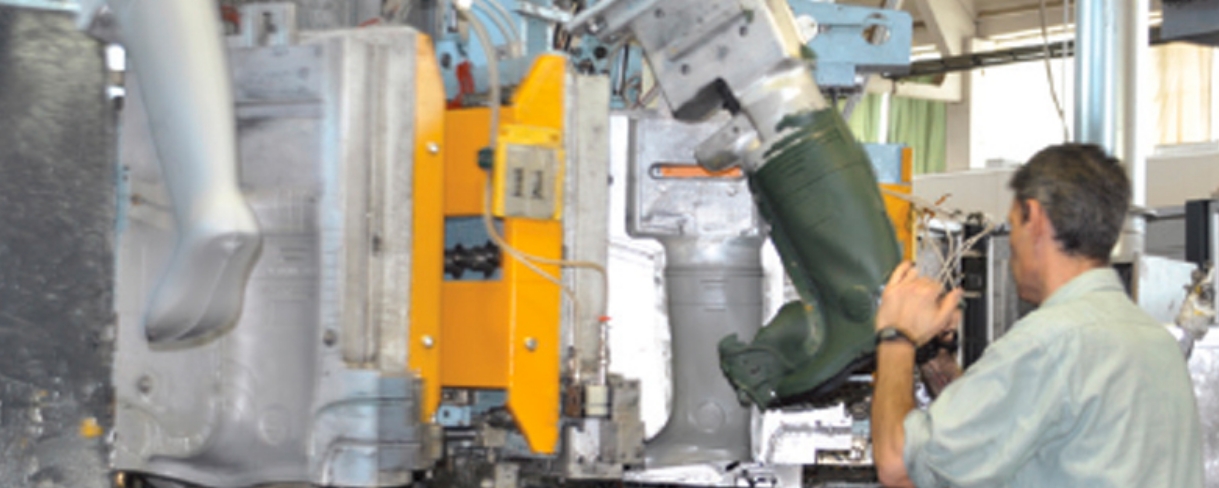
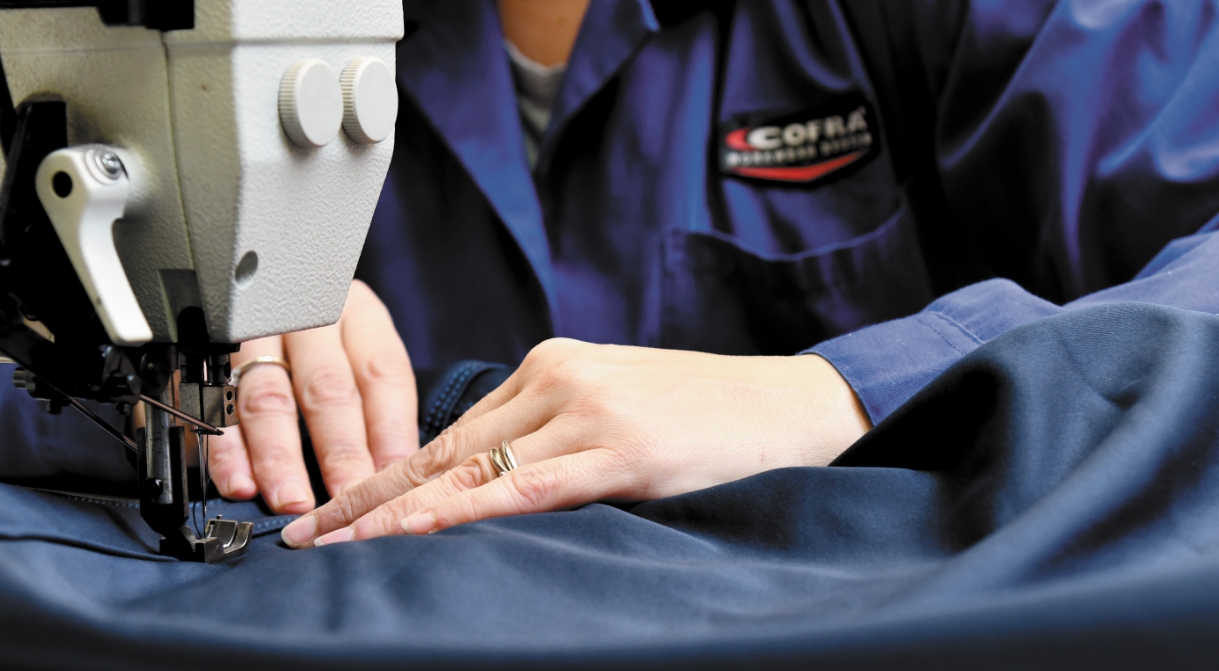
Clothing production100 people employed on two production lines for work clothing in cutting, sewing, and packaging phases.
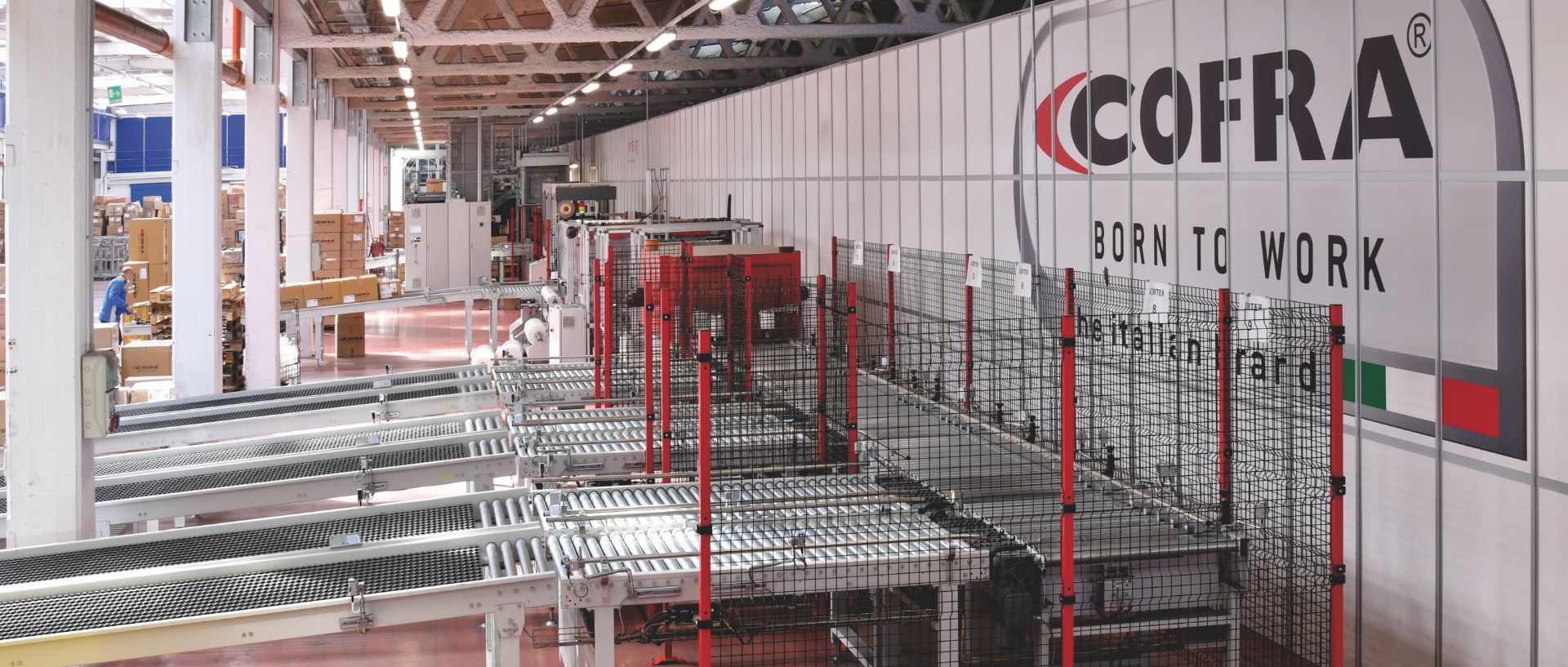
Logistics department
In a highly efficient semi-automated warehouse of 30,600 m², organized according to the most modern logistics criteria, with radiofrequency-managed picking operations, shipments of up to 15,000 pairs of shoes, 6,000 items of clothing, and 5,000 units of gloves, masks, and glasses are coordinated daily.
Automated goods storage systemTo provide the best customer service with minimal processing times and extreme accuracy in order preparation, the company has recently introduced a significant 1650 m² autostore system, with high storage capacity, functioning with a 'goods to man' picking strategy. 33 robots, in a fully automated manner, retrieve the items needed to fulfill each order.
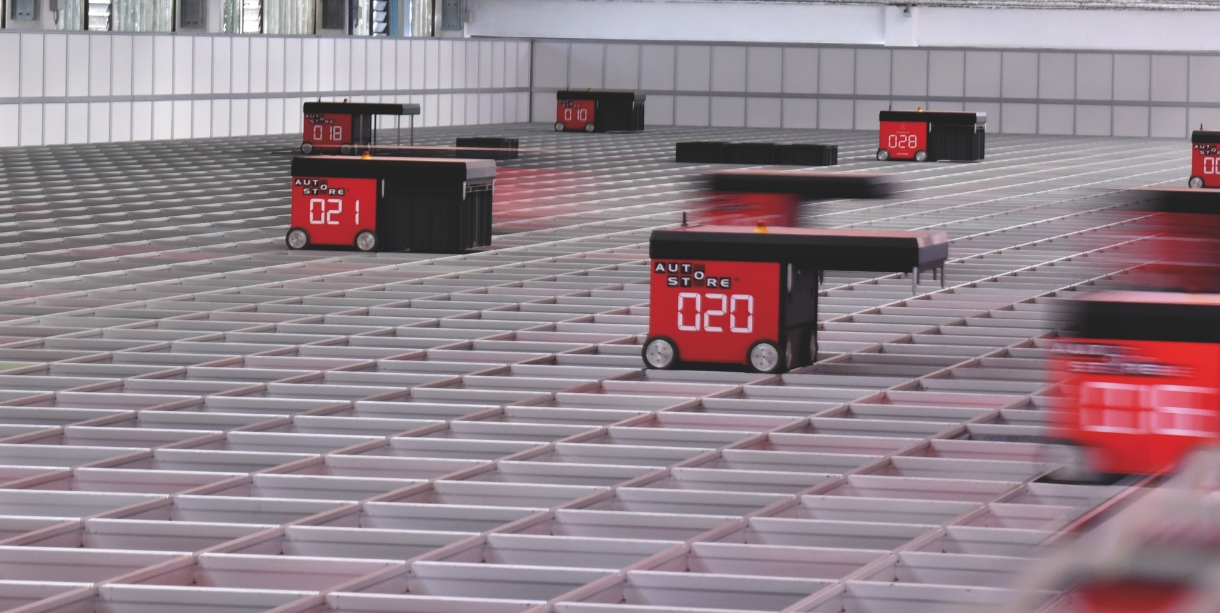
Carton composition
At 6 stations, operators assemble cartons and reintroduce them into the automation phase, which consists of an integrated packaging line where weight, taping, volume calculation, labeling, sealing, and closure take place. The operator's intervention finally allows sorting for subsequent shipment.
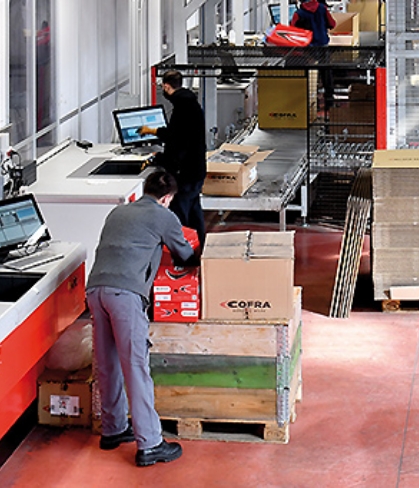
Weight and volume check
Weight and volume are checked to ensure compliance with presumed data on the label attached to the carton. In case of non-compliance, the carton is rejected and rechecked.
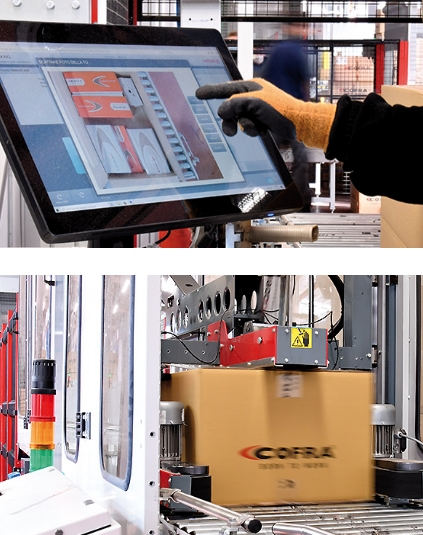
Operational fluidity
Operators are equipped with a finger barcode scanner that ensures smooth operation while keeping hands free. To ensure the best ergonomics and comfortable workspace free from obstacles, the cartons, only when conveyed to the operators, descend from an initial height of 3.20 m to 65 cm, the optimal height.
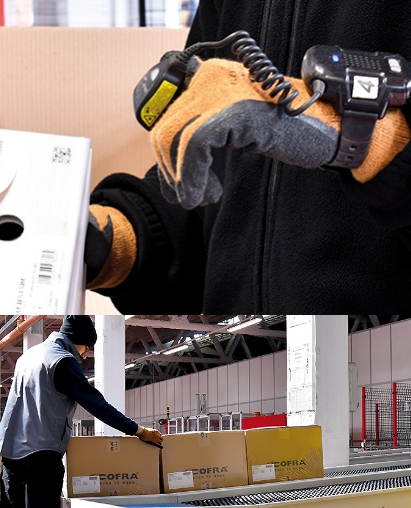